BVN is redefining architecture through circular design and innovation
An interview with Ninotschka Titchkosky, BVN
This article is part of Circular Sydney, ReCo Digital’s initiative to empower sustainable businesses, supported by the City of Sydney.
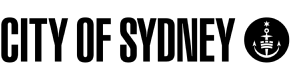
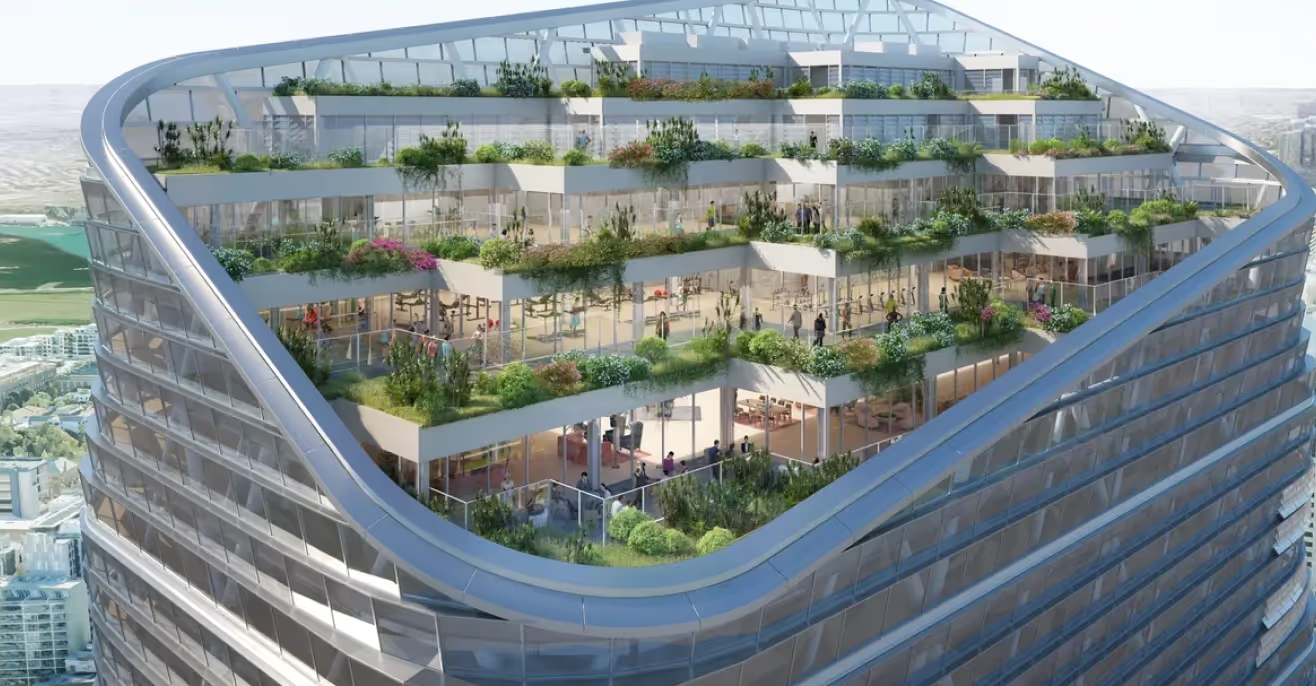
In this interview, Ninotschka Titchkosky delves into how circularity is integrated into BVN's architectural practice, innovative solutions, and how digitalisation helps reduce material consumption.
What is circularity in architecture?
Circularity in architecture is pretty much the same concept as it is anywhere else. It's essentially moving waste into a closed-loop system, away from a linear economic model that relies on the single use of resources.
The construction industry contributes 38 to 40% of all global carbon emissions. It's one of the largest, but also one of the least digitised sectors on the planet. We're well beyond incremental change. We need to radically shift the dial on our approach to construction.
We can't continue to deplete the planet of its resources. We need to consider different approaches to reclaim, reuse and recycle. In the built environment, it's particularly about reducing the resources that we use.
How do you integrate circularity into the work you do at BVN?
Our ultimate goal at BVN is regenerative design. In Australia, there's a very strong connection between regenerative practice, circularity and the way Aboriginal and Torres Strait Islander People think about Country. We must continue to care for Country. We can't keep depleting Country.
When we talk about architecture, we often associate it with new buildings, like our project Atlassian Central. But new buildings actually account for only two to 3% of all buildings on the planet. The rest are existing buildings.
In Europe, most architecture projects are upcycling buildings or adaptive reuse. In very old cities, knocking things down is not considered. We tend to think, everything that has come before us can be knocked down. Or the cheapest option is to knock it down and start over again.
We must look at the bigger picture, and turn our eyes to existing buildings with as much gusto as we put into new buildings. Look at how we can reclaim, upcycle, and reinvent existing buildings.
A great example is Quay Quarter Tower in Circular Quay, designed by 3XN and developed in partnership with BVN. The tower is 50 stories high and grafts onto an existing tower, which is one of the most complicated adaptive reuse projects in the world. By upcycling the original structure, we've saved 7.3 million kilos of carbon, as it already constitutes about 30% of the entire building.
Another example is Queen and Collins in Melbourne. The project is regenerative at a precinct level, including three incredible heritage buildings, a 40-storey tower from the early 90s and surrounding laneways and camp alleys.
If you can save an existing structure, there's already 80% of the carbon banked in. It's important that we can save it, change how the building works, and bring it back to life. This is how we can reduce carbon emissions and achieve regenerative practice.
What we really need is the construction community and clients to come on board. We're at the front end of the problem. We need the whole ecosystem to buy into the concept to make it a reality. That's one of the complicated things about the construction industry and why their carbon emissions are so great. It's a complex industry and getting a grip on it is tricky.
What are the benefits of a circular approach for your clients?
When we were building Queens and Collins, we also had to rethink how it could provide a new work environment with a circular approach.
Usually with commercial buildings, the tenant gets an incentive from the landlord to take on a space and build their fit-out. When the tenant moves out, the landlord retains the fit-out, but would usually dismantle it. Most of the fit-out materials end up in landfill.
We created a pre-designed model that allows the fit-out to be reskinned by the tenant. The owner, GPT Group owns the fit-out, and continues to look after it through the life of the tenancy. That becomes a circular approach and eliminates a massive amount of waste at each tenancy cycle.
So the benefits are two ways:
- For the tenant, they save time in the design process, because they already have a space and service model created for them. They only need to engage as much as they need to.
- For the owner, they no longer give away the cash as incentives. Instead, they keep it in their system, and continue to maintain and evolve the fit-out.
The model has been so successful that we're rolling it out to a total of 50,000 square metres of office space around Australia.
Can you tell us about your innovation, the SR2 air-diffusion system?
The System Reef 2 (SR2) is the world's first robotically 3D printed air-diffusion system to replace traditional air conditioning ducts.
At office buildings, the services infrastructure is incredibly limited and expensive to change. We wanted to rethink the services infrastructure into a more flexible system. Design with less materials to meet our needs.
The first project we did was called Project Octopus, which delivers data and power through fibre optics to the work point. We use it in our Sydney studio.
Then we decided to tackle air conditioning. The air conditioning ducts constitute about 60% of the embodied carbon of the total HVAC (heating, ventilation, and air conditioning) system. Steel ducts and air conditioning ducts haven't evolved in about 90 years.
We ask, do we need a ceiling if we don't have to have one? Can we make the duct system beautiful?
The SR2 is a branched base system with nodes and straights, which can be assembled easily. We took inspiration from frogs because they breathe through their skin. We speed up the robot to create an open pore, so the system becomes a diffuser that breathes on its own.
The system is made from hospital waste plastic, incredibly lightweight. Using 3D printing and robotic fabrication, it uses 90% less embodied carbon compared to traditional steel ducts. At the end of its life, it can be crushed and reprinted.
We're in the process of commercialising it and I'm pretty excited about it.
What can digitalisation help achieve circularity in design and construction?
Digitalisation helps reduce the amount of material we're pulling from the planet through:
- Designing out waste upfront as much as possible.
- Optimising the amount of materials we use.
- Tracking what we're using.
For example, with SR2, the design processes are fully digitised. We use an AI algorithm to do the design, which generates 50,000 options in four hours. We then work out the best fit, develop it ready for production. Every component is inventoried. We know exactly how much embodied carbon is in every component.
Creatively, 3D printing gives us a huge avenue to change traditional ways of working. It helps regenerate the planet, but also creates new aesthetics. It's a new level of craftsmanship that hasn't been economically viable for 100 years or more.
What’s needed to drive circular innovation?
The government has a huge responsibility. One big thing they can do is create an ecosystem for investment in circular innovations. They need to make circularity a key target, so that the market feels more confident and willing to invest.
As a big client for the construction sector, the government needs to mandate circularity and regenerative design in their own projects. They're not aiming high enough at the moment.
We need a lot more capital investment into the built environment. There are investments into prop tech, but not so much into the actual building side. However, as building owners need to report on their ESG targets, they're seeing the importance of circularity and regenerative design. But it's still a slow moving ship.
What's your advice for other architects who're interested in pursuing circularity?
Almost all architectural practices are privately owned. So essentially, it starts at the organisation owners, who can make circularity a strategic focus in their practice. It's got to start at the top. If business owners haven't bought into it, it'll never get real traction. It's a matter of setting.
At BVN, we very much built circularity into our vision and strategic objectives. We took the time to lay the foundations internally, and we keep building on it.
The other way is to keep seeking opportunities, but also create your own. For example, with SR2, we funded the invention in collaboration with UTS. Sometimes, the best place to take those risks is yourself. Using our own studio to experiment is super helpful. But it's not easy. You have to bake it into your vision.
What's your vision for the future?
We have circularity in our objectives and vision. We're still trying to realise many things and we've got a lot of work to do. But if I had a vision of what BVN could bring into this transition, I would think about how we can unite caring for Country with regenerative practice and technology.
If we can do that, we can really develop new ways of seeing the world. The possibilities that are not seen as a burden to us, can be seen as a new awakening to rethink our future beyond where we've been for the last 200 years.
Danling Xiao is the co-founder of ReCo Digital. Danling has an unwavering passion for creativity, spirituality and the pursuit of positive change in the world. Connect with Danling on Linkedin.
Circular Sydney
LIVE 2025
Join 20+ industry leaders and 100 sustainable businesses to learn, connect and transform.
May 2025 | Sydney